
首先,让我们回顾一下压力衰减测试是如何工作的。对被测部件加压(即充入空气或抽真空,直到达到设定的压力或真空),然后与供应压力隔离。然后使用压力传感器监测零件内的压力。随着空气泄漏,压力下降。然后可以根据一段时间内压力的变化来计算泄漏率。
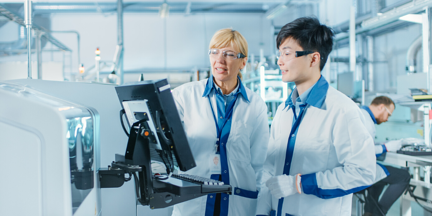
利用压力变化或衰减结果
大量的用户,特别是那些执行任务的用户医疗设备测试,只测试压力变化或压力衰减的结果。在这些情况下,他们选择不做实证研究,以确定什么风量泄漏率导致问题与他们的部分。
相反,他们执行一个简单的实验设计(DOE),试验各种定时器设置,以实现高度一致的最终压力衰减值在一个给定的零件或零件的小样本。然后,他们修复那些一致的计时器设置,测试一些已知的好部分(10到10,000个),并开发出结果的分布曲线,得出平均值和标准偏差值。用户可以选择拒绝标准偏差值的3到6倍的限制。从本质上说,他们已经将“典型的”好部件分类,并在其周围设置了一个窗口。
相对于在部件内部测量的压力变化,泄漏率是实际从部件中流出或离开的空气的体积。尽管有这种区别,但在使用压力衰减测试方法时,这两种技术的测试方法是完全相同的。
移动到泄漏率测量
一旦选定了目标泄漏率,将压力损失拒绝极限转换为泄漏率是非常简单的。它首先使用一个已知的、无泄漏的部件,并有效地教会泄漏测试仪器在没有泄漏的情况下测试的体积。仪器从一个典型的无泄漏部件中记忆这个衰减值,并将其作为零sccm进入存储器。
然后,我们使用相同的已知无泄漏测试件,以及sccm中一个已知值的nist可追溯认证泄漏进行重新测试。仪器被赋予这个认证的泄漏值,当它执行下一次测试时,它会记住泄漏标准造成的额外衰变。
系统现在作为两个校准点——零sccm,理想情况下,如果泄漏标准建立在该部分的泄漏极限附近,sccm中的泄漏极限阈值本身。
为什么采用泄漏率更好
原因有很多。重要的是要记住,根据理想气体定律(PV=nRT),任何给定的测试的压力变化极大地依赖于被测试的加压体积。因此:
- 如果用户在临床功能中使用类似的部件系列,但内部体积可测量不同,则实现泄漏率规范允许用户在整个产品系列(包括测试中的所有相关体积)中轻松拒绝相同的标准(相同的有效孔尺寸)。
- 随着时间的推移,由于磨损,需要更换密封件、工具和连接软管等部件。每次更换都有可能影响被测总容量。
如果使用压力测量,这可能意味着需要重新设置测试的拒绝限值。另一方面,对于泄漏率拒绝极限应用,用户只需执行一个新的两步程序校准,以告知仪器新的压力衰减/变化值。
- 随着生产水平的提高,制造商可能不得不从手工生产转向更加自动化的生产过程。这种转换通常需要改变测试仪器与零件/夹具的接近程度,这必然会改变被测体积。
如果用户只拒绝一个压力变化值,逻辑要求他们重复DOE,以基于测试电路中改变的体积来确定一个新的拒绝压力变化极限。与此形成对比的是,实现了漏率拒绝规范的用户只需要重新教仪器测试的新容量,以达到他们在手动系统上拥有的相同的故障标准。